PREPARING FOR ELECTRIC VEHICLES ALL BEGINS WITH THE PROPER PPE
BY GLENVILLE SINGH
More and more driveways are now adorned with electric or hybrid electric vehicles. Transit agencies are migrating from internal combustion (ICE) to electric buses. Many transport trucking companies have begun the leap forward. As we exit the dawn of the electric vehicle (EV) era and enter the new age of mobility—where EVs are becoming more dominant instead of the novel item they once were—repair technicians are having to pivot from the norms of internal combustion engine repair to learn a new type of propulsion technology.
Yes, the electric drives and zero emissions vehicle is unlike anything the industry has ever seen, and yes, we have certainly made giant strides in a short while with regards to EV repairs as even the aftermarket industry and private shops are getting involved with maintenance and repair of these said vehicles. However, little is said of the other side of the spectrum, the people charged with repairing the body and structures of these electric vehicles after an accident. Why is this? Well, a repair technician can disable the high voltage system before it is sent to the body repair person, but if I were a body repair technician, I would like to have the ability to confirm that the system is truly disabled—not because of mistrust, but because of the severity of not guaranteeing that zero volts are present. Aside from the fact that body technicians have to learn how to navigate working with new materials designed to be lighter to minimize energy usage, and stronger to protect vital parts such as the energy storage systems (ESS) (batteries), they now have to also be concerned with potentially dangerous high voltage wires that can be harmful if voltage is present, making the risk of an electric shock or electrocution always front and center.
But this article is not about the advancement in new materials and the skills body repair personnel need to repair them, instead, I will focus on a more profound topic essential for safety and best practice when performing body repair on electric vehicles: high voltage safety and personal protection. So, what should body repair technicians know when they are about to work on an electric vehicle?
Well, a body repair technician should have at minimum some form of basic high voltage safety training design with a hands-on approach that allows easy synthesizing of information into knowledge through experiential learning.
A body technician should be able to:
✓ Identify high voltage circuits and systems found on the EV.
✓ Understand that an orange wire, no matter how small, should be treated as a live high-voltage wire until otherwise proven.
✓ Identify where on the vehicle the high voltage systems are and the routing of all high voltage wires. This will further enable the technician to prevent the rupture of any high voltage wire while carrying out their repairs.
✓ Know what personal protection equipment (PPE) is required to test for high voltage.
✓ Inspect and test all PPEs before use.
✓ Know how to verify that the high-voltage system is disabled.
Institutions like Centennial College have risen to the challenge of providing training on EVs to technicians and body repair personnel with our industry-leading EV training programs for the automotive and the transit sector. The high-voltage safety course offered by Centennial College would be a great start for a body repair technician who is working on EVs.
So, let’s start from the beginning shall we? A body repair technician needs access to high voltage gloves—class 0 gloves to be exact—and this will protect them from voltages up to 1000 volts AC or 1500 vols DC. These gloves are only required when confirming the presence of high voltage and once zero volts has been confirmed the gloves can be removed. A repairer should also know to inspect high voltage gloves for leaks, expiry dates and shelf life. In terms of tools, the body technicians should know how to use a digital multimeter (DMM) to confirm that all high voltage wires have zero volts before they start working and they should be able to recognize a CAT 111 or CAT 1V DMM and probes which are required for checking high voltage on EVs. To ensure a body technician’s safety, repairers should always approach a high voltage wire as live until it has been tested and confirmed to have zero volts, because of the previously stated statement one should recognize the probability of an arc flash and take the necessary precautions. Here, an arc flash suit rated for the voltage level of the vehicle being worked on should be worn when testing for the presence of high voltage, and a category three arc flash suit will more than suffice as it is rated for 25 Cal/CM2.
Another safety item that a body technician should employ is a second person, often called a spotter, to assist when confirming that the vehicle’s high-voltage system has been disabled. The spotter should have in their procession or close at hand a shepherd’s hook, (an insulated rod usually made from fiberglass or other non-conductive material) used to pull a person away from an electrical source in the event of an electric shock.
As we navigate the EV space, everyone involved has their own set of issues to contend with: manufacturers worry about production, supply, sales, and safety, consumers are concerned about range, cost, and safety, repair technicians have to learn a new set of skills and knowledge all while working safely, recyclers have to know what can be recycled, and how to dispose of what cannot be recycled as environmentally as possible all while being as safe as possible, and so, a body repair technician is no different in that they now have to take on a new role of ensuring that the vehicle they are about to work on is safe by confirming for themselves that the high voltage system on the vehicle is disabled and zero volts are present in all high voltage wires. They must be cautious and cognizant of the fact that the ESS will always have stored energy and as such, they must follow the manufacturer’s recommendations when welding, heating or cutting within close proximity of these ESS.
However, I will leave the welding talk for another day.
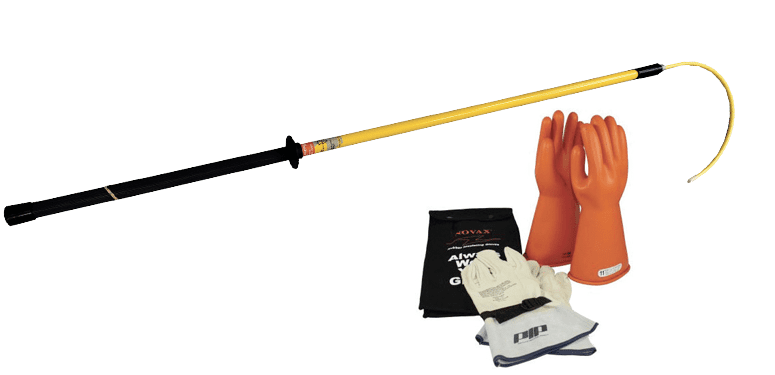
GLENVILLE SINGH has been a professor for the Centennial College School of Transportation, Truck and Coach Department for 15 years. He has also worked as a curriculum developer for the Canadian Automotive Repair and Service Council (CARS) and as a Truck and Coach technician at a few dealerships. Most recently, he has taken on the role of developing and delivering hybrid and electric bus training allowing Centennial College to meet the needs of the transit sector. These hybrid and electric bus courses are the first of their kind offered by a college or training institution, they allow technicians to gain the necessary fundamentals about hybrid and electric buses, allowing them to accelerate their knowledge during OEM training.