NEW DIGS AND FRESH EV REPAIR KNOWLEDGE HAS WEINS COLLISION CENTRE PREPPED FOR THE FUTURE
BY ALLISON ROGERS
You know what they say: beauty is pain. The team at WEINS Collision Repair Centre’s Woodbine Avenue location in Markham, Ontario, knows that very well. The facility recently underwent years of construction, literally trekking through the mud to witness a marvel, marking a milestone in the company’s era of advancement.
These recent—and massive—transformations would not have been possible without two key aspects: a strong, supportive team and network of partners with a collaborative vision, and Victoria Blakeley, bodyshop operations manager, for WEINS Collision Repair Centres. Blakeley has worked with WEINS since 2015, taking the operational reins for both the company’s John Street and Woodbine Avenue locations.
Fresh out of high school, Blakeley began in the auto industry at an assembly plant, where she built cars as a summer job. From there, she worked at another automaker’s plant for 17 years, serving in team lead and quality check positions, where she honed her knack for organization and facilitating smooth operations.
“When it was time to move on, I figured—hey, I used to build cars. Let’s try fixing them. Then I found myself doing accounting for a bodyshop and was interested to see what a career in the collision repair space may look like.”
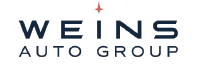
IN THE THICK OF IT
After three years of construction, the WEINS Collision Woodbine Avenue location grew from 3,500 sq. ft. to 18,851 sq. ft., more than doubling its floorspace—not to mention the addition of a sprawling parts space and brand-new equipment.
During a recent visit to the facility, Blakeley showed off her team’s colour-coordinated throughput process and raved about the team’s ability to make things work during the renovations. Ground broke in November 2020, but the collision repairs did not stop through the entire process. Much work was rerouted to the company’s John Street location, but Blakeley recalls her staff had to get creative to ensure high repair standards were maintained in a much, much smaller workspace.
“All of our heavy hits and frame jobs went to John Street. They took our overflow for almost two years, on top of their existing workload. We could not have done this renovation without them and cannot thank them enough for their unwavering support,” said Blakeley.
She also gives credit to her team of technicians, painters and CSRs that stuck by the company’s side through the changes. “I want them to be recognized—the ones that stuck it out alongside us. Everyone not working in the bodyshop was transferred elsewhere during construction, but we stayed here. We must give credit to the dedication of our team.
“I feel like their big sister and their mother all in one,” beamed Blakeley. “I’m so proud that, after everything we went through during the renos, our team has this beautiful, top-of-the-line space to work in.”
The refreshed facility only marked the beginning of revolutionary changes for WEINS.
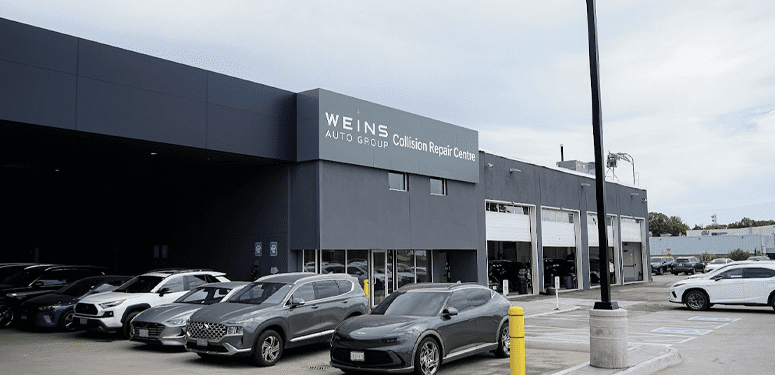
CHARGING UP
The staff at WEINS Collision Repair Centre recently secured its Electric Vehicle Handling Qualified (EVHQ) certification with Certified Collision Care. While the training only requires one appraiser and one bodyperson be trained for EV qualification—meaning two staff from each WEINS Collision Repair Centre location—Blakeley instead opted for the entire team, 21 staff members, undergo the training. WEINS is certified with seven OEMs, many of which offer electric models.
“This is a massive shift for the automotive industry. When you’re working with high voltage vehicles and have no knowledge of their systems, there’s a huge risk of injury. You need high voltage gloves; you need to work on rubber mats, among many other tools—all of which we have and are prepared to use.” The EVHQ training course, administered by Certified Collision Care’s parent company, OEConnection, is designed to equip collision personnel with the information and training to help staff understand the dangers with EVs, as well as the processes and tooling recommended for completing EV repairs. “There’s plenty of new intricacies we need to consider when we have electric vehicles on our production floor. And it can be life or death if you don’t know what you’re doing.
“I want to empower our team,” Blakeley continued. “The more we know, the better we are.”
As for other industry members looking to pursue proper EV repairs and training, Blakeley says knowledge truly is power. “You need to have the knowledge, not just the stamp,” she said. “We at WEINS are not looking to simply check a box by attending this training. We want to be a leader in the collision repair industry. We must ensure our team is capable of repairing these new technologies in adherence with OEM standards and to the confidence of our customers.”
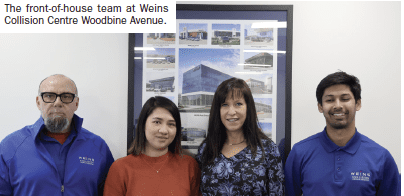
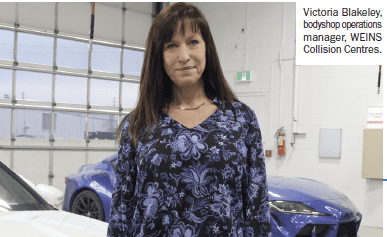
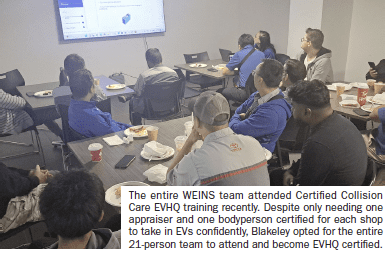
THE ROAD AHEAD
“It’s an exciting, fast-paced time at WEINS Auto Group,” added Blakeley.
Blakeley is not one to keep still for long. It’s only a matter of time before she’s embarked on the next mission.
Currently, WEINS Collision Centre holds OEM certifications for Toyota, Lexus, Honda, Acura, Subaru, Genesis and Hyundai, in addition to a number of direct repair partnerships (DRPs). WEINS Auto Group has two collision centres and aims to keep its customers within the WEINS ecosystem, should they be in need of service. The company touts 14 dealerships and eight brands across Ontario.
Being a dealership facility and part of the Consolidated Collision Services (CCS) network, WEINS prioritizes OEM procedures. In her nine years with WEINS, Blakeley only recalls a single job that didn’t pan out due to insurer-repairer disagreements. She believes it’s only a matter of time before something in the industry gives.
“Someone has to give in. I’ve met with all of our insurance partners recently, warning them that [OEM compliance] is a serious topic and it’s coming their way. It costs a lot to run a bodyshop in 2024. Paint and material costs increased 30 percent in 2022 alone; then you add adhesive, panel bonds, updated equipment. Plus, we must give our staff the appropriate raises,” she added, stressing that some of the WEINS Collision team touts 30-plus years of employment with the company.
“We need a market correction,” concluded Blakeley. “Soon.”