HOW SHOPS CAN PREPARE FOR REFINISHING ELECTRIC VEHICLES
BY SARAH PERKINS
While the fundamental principles of refinishing remain the same, electric vehicles present unique challenges and opportunities due to their distinct construction materials and electrical components. From lightweight materials such as aluminum and composite panels to high-voltage electrical systems, electric vehicles require extra precautions to avoid damage during the refinishing process. Comparatively, advances in paint technology and repair methods increasingly tailored to electric vehicles offer repairers new opportunities for achieving a high-quality finish that enhances both durability and aesthetics. Read below to learn more about what materials and procedures should be taken when refinishing an electric vehicle and see what the industry has to say about what it means to continue to paint for the future.
A TECHNICAL TOOLKIT
When refinishing an electric vehicle, there are several key aspects to consider:
1. Automotive materials: Many electric vehicles use aluminum for lightweighting, which requires specific handling and refinishing techniques.
2. Battery packs: Electric vehicles are equipped with large battery packs that can be vulnerable during repairs. Ensuring these are properly protected is crucial.
3. Electronic systems: Electric vehicles have complex electronic systems that require careful handling to avoid damage. Because of these electric systems, electric vehicles are unable to be cured in paint booths at high temperatures without risking damage.

AN ELECTRIC EFFORT: THE PROCESS OF REFINISHING AN ELECTRIC VEHICLE
1. Assessment and Preparation: Before refinishing an electric vehicle, begin with a thorough inspection of the damage. Pay particular attention to the battery pack, wiring and electronic components. Additionally, it is vital to disconnect the power to the vehicle to ensure that its high-voltage systems are properly shut down. All sensitive electronic components must be protected with sheeting to avoid contamination or damage during the refinishing process.
2. Surface Preparation: Like an internal combustion engine (ICE) vehicle, electric vehicles should be washed to remove any debris or contaminants. This is particularly important when working on the aluminum parts so common to electric vehicles as contaminants can affect paint adhesion. Damaged areas should be sanded to create a smooth surface and material-specific grits should be used to avoid damaging the underlying metal or finish.
3. Priming: As with the grits used, when refinishing an electric vehicle, a primer that is compatible with the vehicle’s materials should also be used. For aluminum, a self-etching primer should be used to ensure proper adhesion. After the primer has cured, sand the surface to ensure a smooth base for the topcoat.
4. Painting and Curing: Global Finishing Solutions (GFS) in “The Electric Slide—How Bodyshops are Safely and Efficiently Stepping into Electric Vehicle Refinishing” notes in greater detail that “because of the powerful battery, electric vehicles are unable to be cured in paint booths at high temperatures. As a result, shops have uncovered more innovative curing methods on electric vehicles, including the implementation of short-wave electric infrared (IR) technology.”
The report continues that “the maximum drying temperatures of high-voltage batteries vary among manufacturers, but statements specify that curing temperatures for electric and hybrid vehicles should not exceed 140 to 150 degrees Fahrenheit.”
“Since electric vehicles are unable to be cured in a normal paint booth cure cycle, an extended low cure cycle is typically used. However, an extended low cure cycle doubles the bake time, reducing overall throughput and significantly slowing down operations. Even when using an express-style clear coat, paint quality issues arise—a problem that is magnified when working on luxury vehicles. To quickly cure electric vehicle without causing damage, the best solution,” for GFS is short wave electric IR technology.”
Using these systems, “temperatures on the exterior of the vehicle might eclipse 200 degrees, but the interior of the vehicle will not surpass 100 degrees. Therefore, the battery will not overheat, protecting the vehicle and the technician.” As a result, “electric IR technology reduces drying time for both the preparation and painting phases of the repair process. Short wave electric IR can cure up to three layers with one pass, without skinning or solvent popping the top layer.”
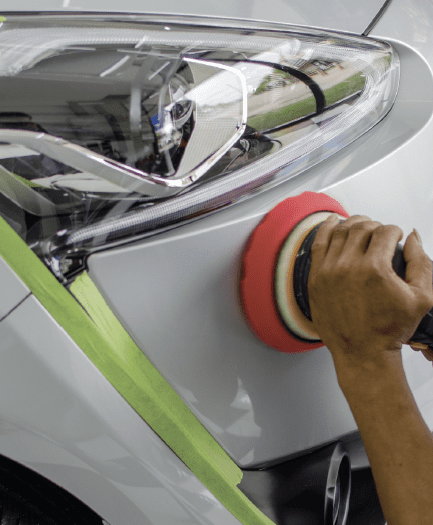
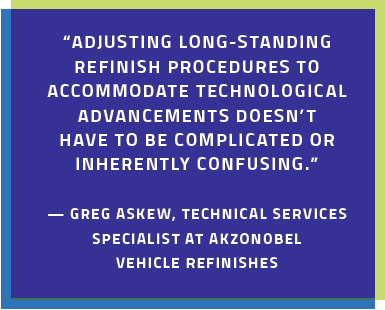
AN EXPERT TOUCH
We reached out to experts from the industry to find out more about what steps should be taken when refinishing an electric vehicle. When speaking with Greg Askew, Technical Services Specialist at AkzoNobel Vehicle Refinishes, he commented that with the increase in technologically advanced vehicles, “longstanding repair procedures may no longer align with the advancement incorporated in new vehicles.”
This is because, “the elevated temperatures commonly used when force-drying an automotive system have the potential to cause thermal damage to the high-voltage battery. The possibility of booth curing temperatures being too high is something that technicians rarely, if ever, contemplated in the past.”
Askew further confirmed that “high-voltage batteries that store the energy needed to propel electric vehicles are sensitive to extreme temperatures and may be irreversibly damaged or destroyed if the proper procedures are not followed when performing repair and refinish operations. All vehicle repair plans should begin by referencing the OEM procedures and following them throughout all phases of the repair.”
For Askew, it is also “critical for the repairer to be fully informed of the necessary processes and precautions; not only to protect the vehicle battery, but to minimize the chance of a life-threatening explosion or fire.”
When asked about the specific tools and technology to consider when working on an electric vehicle, Askew noted that “the vehicle’s battery temperature is moderated by utilizing various battery thermal management system (BTMS) technologies, dependent on manufacturer. These cooling and heating systems are designed to maintain the battery temperature within the optimal functioning range, which contributes to the expected performance and lifespan of the battery cells.”
“Electric and hybrid-electric vehicle repairs may often require disconnecting the power sources, thereby disabling the active BTMS and rendering the high-voltage battery unprotected from temperature extremes like those that occur when curing the paint in the booth. Even if the BTMS is functional, concerns for battery heat exposure remain and the repairer must still follow the parameters provided by the OEM to prevent possible thermal damage to the battery system.”
“It is critical to consider factors such as bake temperature, surface temperature and ramp time when planning the refinish procedure, as they are directly related to the time and temperature parameters the OEM guidelines will provide,” Askew said. “After reviewing and understanding the time and temperature parameters set by the OEM, there are often several paint product-system selections that can be effective in reducing bake time, temperature or both.” “Some clear coat systems are designed specifically for low bake temperatures or ambient air-dry conditions. Others offer various bake times and temperatures depending on hardener and accelerator selections.”
“Another option to consider,” Askew continued, “is when the vehicle will be painted. Scheduling the EV as the last job of the day may allow for an extended dry time at a reduced booth temperature or an overnight drying period at ambient temperatures, which will eliminate the elevated temperature concern. If choosing this option, always ensure the ambient temperature will be high enough to cure the paint as curing virtually stops at low temperatures.” On this note, Askew highlighted how “depending on the specifics of the repair and the equipment available, infrared curing may be an excellent solution. Most clear coat technical data includes a guidance on infrared. When using infrared, the heat energy is localized and, in most solutions, will not directly impact the battery system. However, through this process, it is critical to be aware of the locations of high-voltage batteries to avoid inadvertently overheating the battery.”
With these technological considerations and procedures in mind, Askew concluded that while the automotive repair industry may be at a learning curve, ultimately, “adjusting long-standing refinish procedures to accommodate technological advancements doesn’t have to be complicated or inherently confusing.”
“The most important part of this challenge is awareness. Creating a repair plan with OEM repair procedures as the foundation is key. Due to the nature of collision repairs, body technicians have long been required to follow the vehicle manufacturer’s procedures. Now, it’s time to ensure the refinisher is included in the plan.”
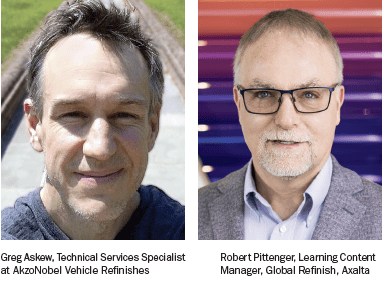
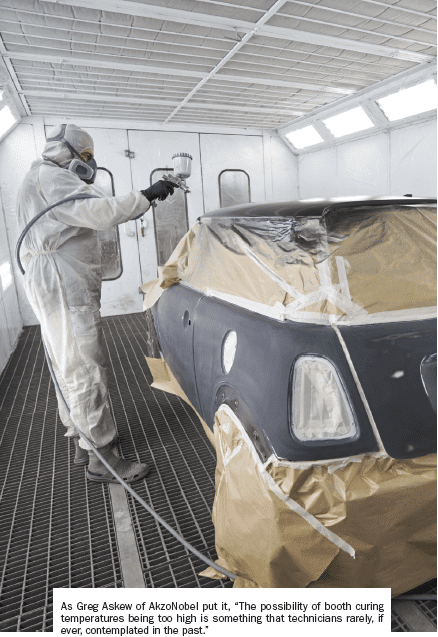
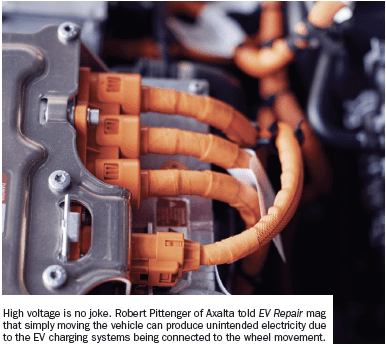
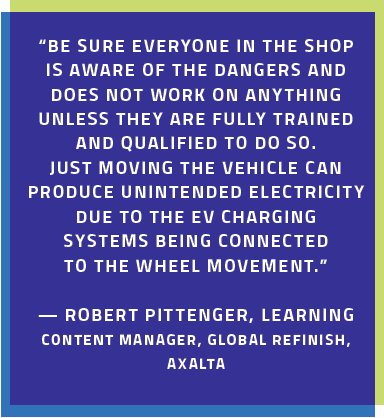
Moreover, when speaking with Robert Pittenger, Learning Content Manager, Global Refinish, Axalta stressed that first and foremost, “the main requirements when refinishing an electric vehicle is to practice safety from start to finish.”
“Electric vehicles have high-voltage systems that are different from internal combustion engines and as a result, have specific time and temperature limits.”
Furthermore, like Askew, Pittenger outlined how “the main concern with EVs is the high-voltage systems and the possibility of unintended electrical discharge. The first step when working on an electric vehicle is to make sure there is no damage to the high-voltage system. The second step—check that the vehicle cannot be switched on accidentally. There are protocols for each individual vehicle, including receiving the vehicle, moving, disassembly and disconnecting the power if needed.”
“This involves,” Pittenger continued, specialized training, PPE and equipment. Be sure everyone in the shop is aware of the dangers and does not work on anything unless they are fully trained and qualified to do so. Just moving the vehicle can produce unintended electricity due to the EV charging systems being connected to the wheel movement. The use of specialized wheel dolly or tire skates may be needed to ensure the wheels don’t turn when moving it to different stations.”
In terms of curing and refinishing procedures for electric vehicles, Pittenger agreed that “lower bake temperatures are especially helpful, so whenever possible, using products that do not require high temperature baking or have a shorter bake time is also helpful. Products that offer fast cure times and low energy are also very helpful for productivity due to the ability to cure in less time at lower temperatures.”
“Ultimately, each manufacturer, and even each vehicle model, may have different requirements for drying or baking temperatures. Be sure to check the OEM procedures. In general, a maximum of 140 degrees Fahrenheit or 60 degrees Celsius for 45 minutes is common, but always check each manufacturer to be sure that you stay within an allowable limit. Otherwise, there is the risk that you will compromise the battery or worse, destroy the battery and possibly cause a safety incident.”
When asked about how repairers should navigate around the high-voltage battery while working on an electric vehicle, Pittenger concluded that it’s all about being informed and staying up to date on vehicle knowledge.
“Electric vehicles should be assigned to an EV specialized technician and dedicated EV bay. Limit contact with the vehicle to only those that are fully trained on the hazards. Often, there are also ADAS procedures that are critical for proper repairs. Instructions with ADAS and OEM procedures specific to the vehicles should be provided to the specialized EV technician about the vehicle before starting a refinishing job.”
In this way, for both Askew and Pittenger, while the future of electric vehicles may present high voltage hurdles that repairers will need to overcome, the future is not as daunting as it perhaps seems so long as repairers also practice procedure and accept the learning curve of painting for the future.